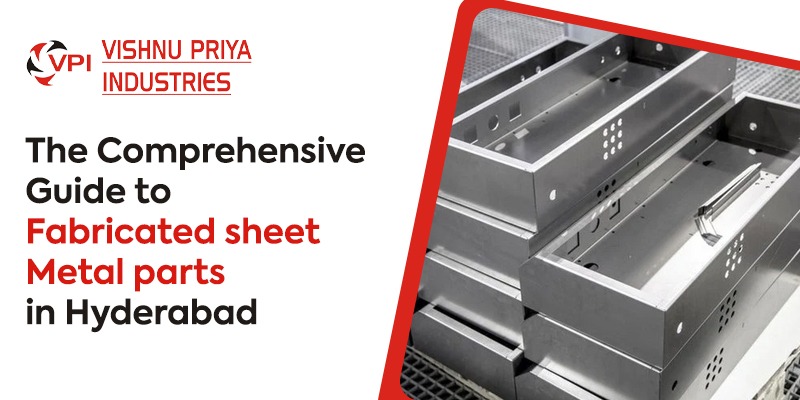
The Comprehensive Guide to Fabricated sheet metal parts in Hyderabad
Fabricated sheet metal parts in Hyderabad
Sheet metal fabrication is a vital manufacturing process that involves transforming flat sheets of metal into various shapes, structures, and components through cutting, bending, welding, and other techniques. This process has been around for centuries, but modern advancements in technology have made it more precise, efficient, and versatile than ever before. At its core, sheet metal fabrication involves taking thin, flat sheets of metal (usually ranging from a few millimeters to several inches in thickness) and manipulating them into desired shapes and designs. The most common metals used in Fabricated sheet metal parts in Hyderabad include steel, aluminum, stainless steel, copper, brass, and galvanized iron, each with its unique properties and applications.
Fabricated sheet metal parts Works in Hyderabad
The importance of fabricated sheet metal parts cannot be overstated in today’s world. These components are ubiquitous, playing crucial roles in a wide range of industries and applications. From the sleek exterior panels of automobiles to the intricate structures of aircraft, from the sturdy frames of buildings to the compact housings of electronic devices, fabricated sheet metal parts are everywhere, providing strength, durability, and aesthetic appeal. We at Vishnu Priya Industries offer the best Fabricated sheet metal parts Works in Hyderabad
In the automotive industry, sheet metal fabrication is essential for producing car bodies, frames, engine components, and numerous other parts. The aerospace sector relies heavily on lightweight yet robust sheet metal components for aircraft fuselages, wings, and other structures. The construction industry benefits from fabricated sheet metal for roofing, siding, ductwork, and architectural elements. Manufacturing plants utilize sheet metal enclosures, cabinets, and racks to house and protect various equipment and machinery.
Even in the healthcare industry, fabricated sheet metal parts are indispensable, used in the construction of medical equipment, hospital furniture, and other critical components. Consumer products, such as appliances, furniture, and electronics housings, also heavily incorporate sheet metal fabrication for their aesthetic appeal, durability, and functionality.
Understanding Sheet Metal Fabrication
To fully grasp the world of fabricated sheet metal parts, it’s essential to understand the fundamentals of sheet metal fabrication itself. This process involves transforming flat sheets of metal into various shapes, components, and structures through a combination of cutting, bending, welding, and other techniques.
1. Steel: One of the most widely used materials in sheet metal fabrication, steel offers exceptional strength, durability, and cost-effectiveness. It is available in various grades, including mild steel, carbon steel, and high-strength alloy steels, catering to different application requirements.
2. Aluminum: Lightweight yet sturdy, aluminum is a popular choice for applications where weight is a critical factor, such as in the aerospace and automotive industries. It is corrosion-resistant, easy to work with, and can be anodized or coated for enhanced aesthetics and protection.
3. Stainless Steel: Renowned for its resistance to corrosion, stainless steel is a versatile material commonly used in industries such as food processing, chemical processing, and healthcare. Its durability and easy maintenance make it a preferred choice for applications requiring hygiene and cleanliness.
4. Copper: With its excellent thermal and electrical conductivity, copper is often used in the fabrication of electrical components, heat exchangers, and decorative architectural elements.
5. Brass: An alloy of copper and zinc, brass offers a unique combination of strength, corrosion resistance, and aesthetics, making it suitable for decorative applications, plumbing fixtures, and various industrial components.
6. Galvanized Steel: By coating steel with a protective layer of zinc, galvanized steel offers enhanced resistance to corrosion and improved durability, particularly in outdoor or harsh environments.
The fabrication of sheet metal parts involves a variety of processes, each designed to achieve specific shapes, features, and characteristics. Some of the most common sheet metal fabrication processes include:
1. Cutting: Sheets of metal are cut into desired shapes and sizes using various techniques such as laser cutting, plasma cutting, water jet cutting, shearing, or stamping. These cutting methods allow for precise and intricate designs while minimizing material waste.
2. Bending: Once cut, the sheet metal is often bent or formed into three-dimensional shapes using machines like press brakes, roll formers, or folding machines. Bending is a crucial step in creating components with specific angles, curves, or profiles.
3. Welding: To join multiple pieces of sheet metal together, various welding processes are employed, such as MIG (Metal Inert Gas) welding, TIG (Tungsten Inert Gas) welding, or spot welding. Welding ensures strong, durable connections between the fabricated components.
4. Punching and Stamping: These processes involve using specialized tools or dies to create holes, cutouts, or embossed features in the sheet metal. Punching and stamping are commonly used for creating vents, openings, or decorative patterns in the final product.
5. Finishing: After fabrication, sheet metal parts may undergo various finishing processes to enhance their appearance, durability, or functionality. These processes include painting, powder coating, plating, anodizing, or polishing, depending on the specific application and requirements.
Applications and Industries
The applications of fabricated sheet metal parts are vast and diverse, spanning numerous industries and sectors. From the sleek lines of automobiles to the soaring structures of aircraft, from the sturdy frames of buildings to the compact housings of consumer electronics, sheet metal fabrication plays a crucial role in shaping our modern world.
Automotive Industry:
The automotive industry is one of the largest consumers of fabricated sheet metal parts. Car bodies, frames, engine components, and numerous other automotive parts are meticulously crafted from sheet metal. The outer body panels, which give vehicles their distinctive shapes and aesthetics, are formed through intricate sheet metal fabrication processes. Additionally, structural components like frames, chassis, and engine cradles rely on the strength and durability of fabricated sheet metal parts to ensure vehicle safety and performance.
Aerospace Industry:
In the aerospace sector, where lightweight yet robust materials are paramount, sheet metal fabrication takes center stage. Aircraft fuselages, wings, and other structural components are often constructed from carefully fabricated sheet metal parts. The aerospace industry demands exceptional precision and adherence to stringent quality standards, making sheet metal fabrication a critical process for ensuring the reliability and safety of aircraft.
Construction Industry:
The construction industry heavily relies on fabricated sheet metal parts for a variety of applications. Roofing systems, siding, ductwork, and architectural elements are commonly made from sheet metal due to its durability, weather resistance, and versatility in design. Sheet metal fabrication enables the creation of customized components tailored to specific building requirements, contributing to both the functionality and aesthetic appeal of structures.
Manufacturing Industry:
In manufacturing facilities and plants, fabricated sheet metal parts play a vital role in housing and protecting various equipment and machinery. Enclosures, cabinets, racks, and other protective structures are often crafted from sheet metal to provide durability, resistance to harsh environments, and ease of maintenance. These fabricated components ensure the efficient and secure operation of manufacturing processes while also contributing to workplace safety.
Healthcare Industry:
The healthcare industry benefits greatly from the versatility of sheet metal fabrication. Medical equipment, hospital furniture, and other critical components are frequently fabricated from sheet metal due to its hygienic properties, corrosion resistance, and ability to withstand frequent cleaning and sterilization. From surgical tables to medical device housings, sheet metal fabrication plays a vital role in ensuring the reliable and safe delivery of healthcare services.
Consumer Products:
Fabricated sheet metal parts are ubiquitous in the consumer products industry, encompassing a wide range of applications. Appliances, such as refrigerators, ovens, and washing machines, rely on sheet metal components for their structural integrity and aesthetic appeal. Furniture pieces, decorative elements, and even electronic housings often incorporate fabricated sheet metal parts, combining durability with sleek designs.
These are just a few examples of the countless industries and applications that rely on fabricated sheet metal parts. From the smallest components to large-scale structures, sheet metal fabrication has become an indispensable manufacturing process, shaping the products and environments that surround us in our daily lives. As technological advancements continue to enhance fabrication techniques, the versatility and applications of sheet metal parts will continue to expand, driving innovation across various sectors.
Sheet Metal Fabrication Processes
The fabrication of sheet metal parts involves a diverse array of processes, each designed to achieve specific shapes, features, and characteristics. From cutting and bending to welding and finishing, these processes work in harmony to transform flat sheets of metal into intricate, three-dimensional components. Let’s delve into the most common sheet metal fabrication processes:
Cutting Processes:
Cutting is often the first step in sheet metal fabrication, as it involves separating the flat metal sheets into the desired shapes and sizes. Several cutting techniques are employed, each with its unique advantages and applications:
1. Laser Cutting: This precise and efficient cutting method uses a high-powered laser beam to cut through the metal sheet. Laser cutting offers exceptional accuracy, allowing for intricate designs and tight tolerances. It is suitable for a wide range of metals and thicknesses.
2. Plasma Cutting: In plasma cutting, an ionized gas is used to create a hot, conductive plasma arc that cuts through the metal sheet. This process is known for its speed, versatility, and ability to cut thicker materials with relatively straight edges.
3. Water Jet Cutting: This cutting technique utilizes a high-pressure stream of water, sometimes mixed with abrasive materials, to cut through the metal sheet. Water jet cutting is ideal for cutting complex shapes, intricate details, and thick materials without creating heat-affected zones.
4. Shearing and Stamping: These traditional cutting processes involve using mechanical force to shear or stamp the metal sheet into the desired shapes. Shearing is suitable for creating straight cuts, while stamping is often used for mass-producing simple shapes and components.
Bending Processes:
Once the metal sheets are cut into the required shapes, bending processes are employed to create three-dimensional forms and contours. Bending is a crucial step in fabricating components with specific angles, curves, or profiles. Common bending processes include:
1. Press Brake Bending: This process uses a press brake machine to bend the metal sheet along a straight line. Press brake bending is versatile and can accommodate a wide range of materials, thicknesses, and bend angles.
2. Roll Bending: In roll bending, the metal sheet is passed through a series of rollers that gradually bend the material into curved or cylindrical shapes. This process is often used for creating pipes, tubes, or curved architectural elements.
3. Folding and Seaming: Folding involves bending the metal sheet at specific angles to create sharp corners or edges while seaming joins two or more folded sections together to form enclosed shapes or structures.
Welding Processes:
To join multiple pieces of sheet metal together, various welding processes are employed. Welding ensures strong, durable connections between the fabricated components and is often a critical step in creating larger structures or assemblies. Common welding processes in sheet metal fabrication include:
1. MIG (Metal Inert Gas) Welding: Also known as GMAW (Gas Metal Arc Welding), MIG welding uses a continuous wire electrode and an inert gas to create the weld. It is widely used for its versatility, speed, and ability to weld various metals, including steel, aluminum, and stainless steel.
2. TIG (Tungsten Inert Gas) Welding: In TIG welding, an arc is struck between a non-consumable tungsten electrode and the metal workpiece, creating a precise, high-quality weld. This process is commonly used for welding thin materials, intricate joints, and applications requiring exceptional weld quality.
3. Spot Welding: Spot welding is a process that uses electrodes to create localized welds at specific points, joining two or more metal sheets together. This technique is commonly used in automotive manufacturing and other applications where spot welds are sufficient for joining components.
Punching and Stamping Processes:
These processes involve using specialized tools or dies to create holes, cutouts, or embossed features in the sheet metal. Punching and stamping are commonly used for creating vents, openings, or decorative patterns in the final product. CNC (Computer Numerical Control) punching machines and hydraulic presses are often employed for accurate and consistent results.
Finishing Processes:
After fabrication, sheet metal parts may undergo various finishing processes to enhance their appearance, durability, or functionality. These processes include:
1. Painting and Powder Coating: Applying paint or powder coatings can provide corrosion resistance, improve aesthetics, and add a protective layer to the fabricated parts.
2. Plating: Metal plating processes, such as zinc plating, nickel plating, or chrome plating, can enhance corrosion resistance, improve wear resistance, or provide a decorative finish.
3. Anodizing: Anodizing is a process that creates a protective oxide layer on the surface of metals like aluminum, improving corrosion resistance and allowing for various color finishes.
4. Polishing and Brushing: These processes can create a smooth, shiny, or brushed finish on the surface of the fabricated parts, enhancing their visual appeal and reducing the risk of corrosion.
Benefits of Fabricated Sheet Metal Parts
Fabricated sheet metal parts offer a multitude of benefits that make them a preferred choice across various industries.
One of the primary benefits of fabricated sheet metal parts is their cost-effectiveness. Sheet metal materials are relatively inexpensive compared to other materials like plastics or composites, especially when considering their strength-to-weight ratio. Additionally, the fabrication processes themselves are efficient and can be scaled to meet varying production demands, further contributing to cost savings. Sheet metal fabrication offers remarkable design flexibility, allowing for the creation of intricate shapes, curves, and features. With advanced cutting and bending techniques, manufacturers can bring even the most complex designs to life, enabling innovation and customization tailored to specific application requirements.
Fabricated sheet metal parts are renowned for their durability and structural strength. Materials like steel, aluminum, and stainless steel have inherent toughness and resistance to impact, wear, and fatigue. This durability ensures a long service life for the fabricated components, reducing the need for frequent replacements and minimizing maintenance costs. Many sheet metal materials, such as stainless steel and aluminum, offer excellent corrosion resistance properties. This resistance to rust, oxidation, and chemical attacks makes fabricated sheet metal parts ideal for use in harsh environments, outdoors, or in corrosive applications like chemical processing or marine environments. While offering exceptional strength and durability, fabricated sheet metal parts can still be remarkably lightweight, especially when using materials like aluminum. This combination of strength and low weight is highly desirable in industries like aerospace, automotive, and construction, where weight savings translate into improved fuel efficiency, reduced emissions, and easier transportation and installation.
Choosing a Sheet Metal Fabrication Partner
- Look for a fabricator with extensive experience in the industry, as well as specialized knowledge in working with your specific materials and applications. Experienced fabricators can offer valuable insights and recommendations to optimize your designs and processes.
- Assess the fabricator’s capabilities in terms of the processes they offer, the materials they can work with, and the equipment they have at their disposal. Ensure they have the necessary resources to meet your project requirements, including cutting-edge technology for precision and efficiency.
- Prioritize fabricators with robust quality control processes in place, such as ISO certifications, adherence to industry standards, and non-destructive testing methods. These measures ensure consistent quality and minimize defects or non-conformances.
- Consider the fabricator’s production capacity and their ability to meet your desired lead times and delivery schedules. A reliable partner should be able to handle your volume requirements without compromising quality or timeliness.
Vishnu Priya Industries qualifies for all the above qualities.
Advantages of Working with a Reputable Fabricator:
Partnering with a reputable and experienced sheet metal fabricator offers numerous advantages, including:
- Reputable fabricators have a wealth of knowledge and experience that can guide you through the entire fabrication process, from design to production, ensuring optimal results.
- Established fabricators prioritize quality control and have stringent processes in place to ensure consistent quality, minimizing the risk of defects or non-conformances.
- Experienced fabricators can often identify opportunities for cost savings through efficient material utilization, process optimization, and streamlined workflows, without compromising quality.
- A reputable partner will provide reliable support throughout the project, addressing any concerns or issues that may arise and working collaboratively to find solutions.
Final words
Fabricated sheet metal parts are essential components that shape our modern world, from the sleek designs of automobiles to the sturdy structures of buildings. Throughout this comprehensive guide, we have explored the intricacies of sheet metal fabrication, its diverse applications, and the processes involved in transforming flat sheets of metal into intricate, three-dimensional components.
Fabricated sheet metal parts are the unsung heroes of our modern world, enabling countless products, structures, and systems to function seamlessly. As we move forward, it is essential to stay informed about the latest developments and innovations in sheet metal fabrication to ensure that we continue to meet the evolving needs of various industries.
When seeking fabricated sheet metal parts, it is highly recommended to partner with a reputable and experienced fabricator like Vishu Priya Industries who can provide expertise, quality assurance, and reliable support throughout the entire process.